One. Polyvinyl chloride (PVC)
PVC is a heat-sensitive plastic, generally divided into conical twin screw barrel,hard and soft. Less than 10% of the plasticizer added to the raw material is lightweight, and more than 30% is ductile.
a No obvious melting point, 60 becomes soft, 100~150 is a point bomb state, 140 dissolves and decomposes at the same time, 170 decomposes rapidly, the softening point is close to the decomposition point, and the decomposition is released from the HCI gas.
b Poor thermal stability, temperature and time all lead to decomposition and poor fluidity.
For injection molded PVC screws, please note the following:
aTemperature control is strictly controlled, and the screw design should use low shear as much as possible to prevent overheating.
b Screws and pipes should be protected from corrosion.
c The injection molding process must be strictly controlled.
D Generally, screw parameters are L/D=16 to 20, h3=007De=1.6 to 2, L1=40%L, L2=40%L.
e is the material of the small intestine, the trade ring, and the taper of the head is 20 to 30. In the case of high requirements for soft rubber products, infinite segment and separate screws can be used. This type of screw is more suitable for rigid PVC: To adjust the temperature, add cooling water or oil holes inside the supply section screw, and add a cold water bucket or oil flow to the pipe.
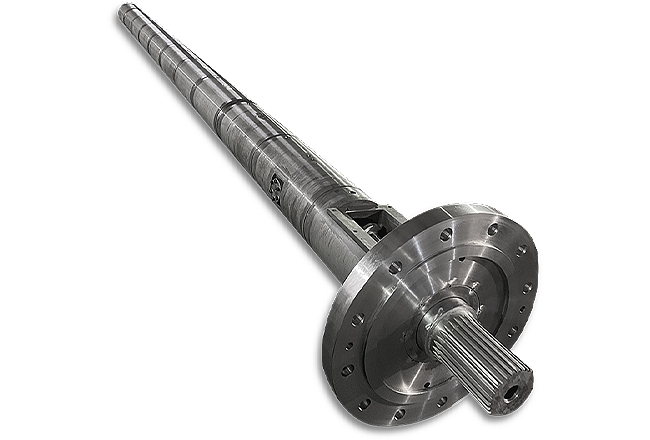
Two: Polycarbonate (PC)
a: Amorphous plastic, no obvious melting point, glass transition temperature 140~150C, melting temperature 215~225C, molding temperature 250~320C.
b: High viscosity, sensitive to temperature, good thermal stability in the normal processing temperature range. Long stays below 300 will basically not decompose. It starts to decompose after exceeding 340. Viscosity is less affected by shear rate.
c: Strong absorption.
For injection molded PC screws, please note the following:
a: For the characteristics of good thermal stability and high viscosity, in order to improve the plasticizing effect, please choose the largest aspect ratio as possible. 26 is generally used. Due to the large melt temperature range, the compression section may become longer, so use gradient screws. L130%L, L2=46% l3360
b: The compression ratio S gradient A must be suitable for the melt velocity, but the microbath velocity cannot be calculated accurately at present. Gradient A values can be based on values of moderate skewness, according to the properties that PC can melt from 225 to 320. When L2 is large, the general gradient screw e=2~3, A-;
C: High viscosity and strong absorption, so before the homogenization section and after the compression section, the film blowing screw and barrel manufacturers believe that a mixing structure can be added to the screw to enhance the disintegration of the solid bed and at the same time convert the moisture trapped in it into gas. .
D: Other parameters (for example, E, S, A and the clearance of the tube can be the same as other conventional screws.
Three: plexiglass (PMMA)
A: The glass transition temperature is 105, the melting temperature is greater than 160, the decomposition temperature is 270, and the molding temperature range is very wide.
B: High viscosity, poor fluidity and good thermal stability.
C: Absorbency is strong.
For injection-molded PMMA screws, please note the following:
A: Choose a gradient color screw with an aspect ratio of 20~22. According to the accuracy of product molding, generally L1=40%L, L2=40%L.
B: The compression ratio E is usually selected from 2.3 to 2.6.
C: Has a certain hydrophilicity, so a mixed ring structure is used in front of the screw.
D: Other parameters can usually be designed as ordinary screw, and the gap between it and the tube should not be too small.
Post time: Dec-22-2022